BETWEEN 1857 and 1980 a total of 12 iron works operated in Northamptonshire. Half ceased production in the 19th century but 11.6Mt of iron had been produced by 1920. Those that survived into the 20th century were: Irthlingborough (1866 – 1929), Hunsbury Hill (1873 – 1936), Islip (1871 – 1945), Cransley of Kettering (1875 – 1956), Wellingborough (1885 – 1961) and Corby (1910 – 1980). This latter works still operates today, no longer making steel but continuing to produce tube as part of Tata Steel Europe.
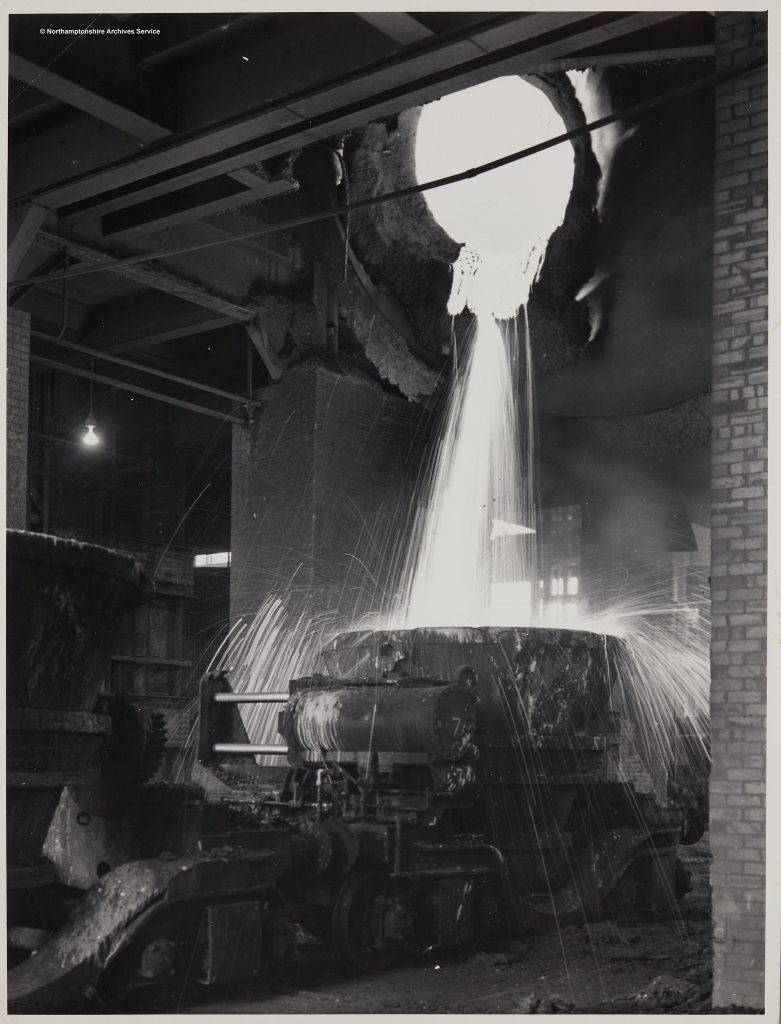
Mouton metal being poured . scan by Northants archives
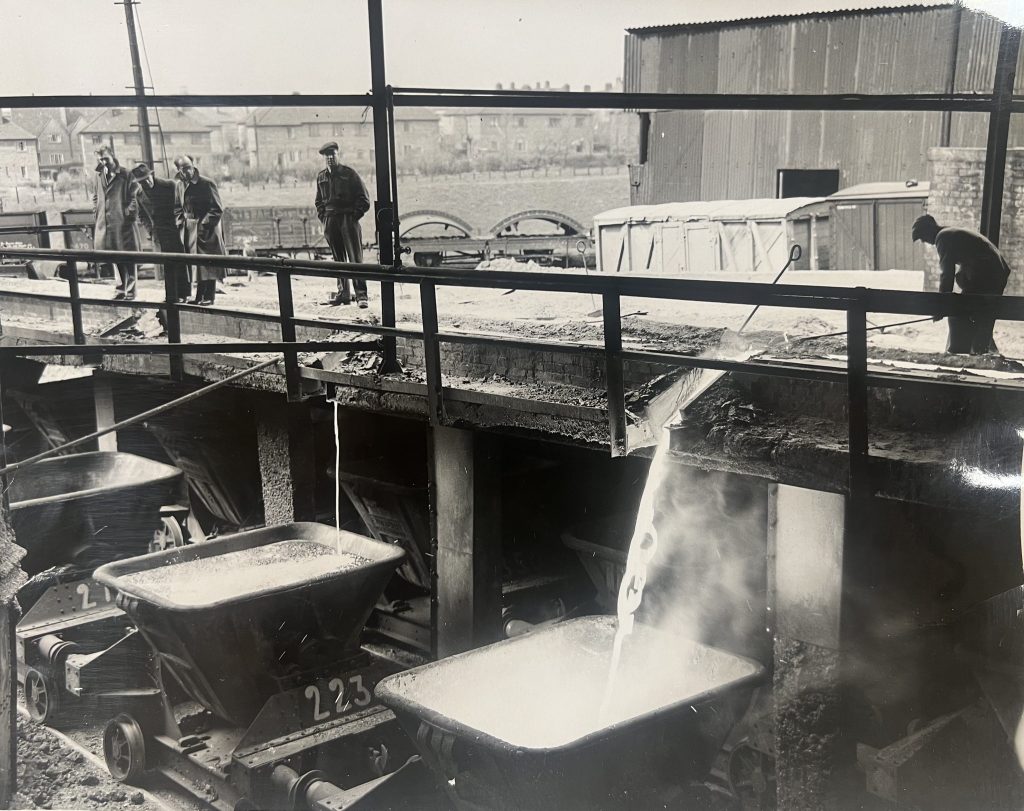
The above image is believed to of been taken at the Kettering ironworks. The molten liquid iron is probably going to be moved to be taken to mould into pigs .
Islip
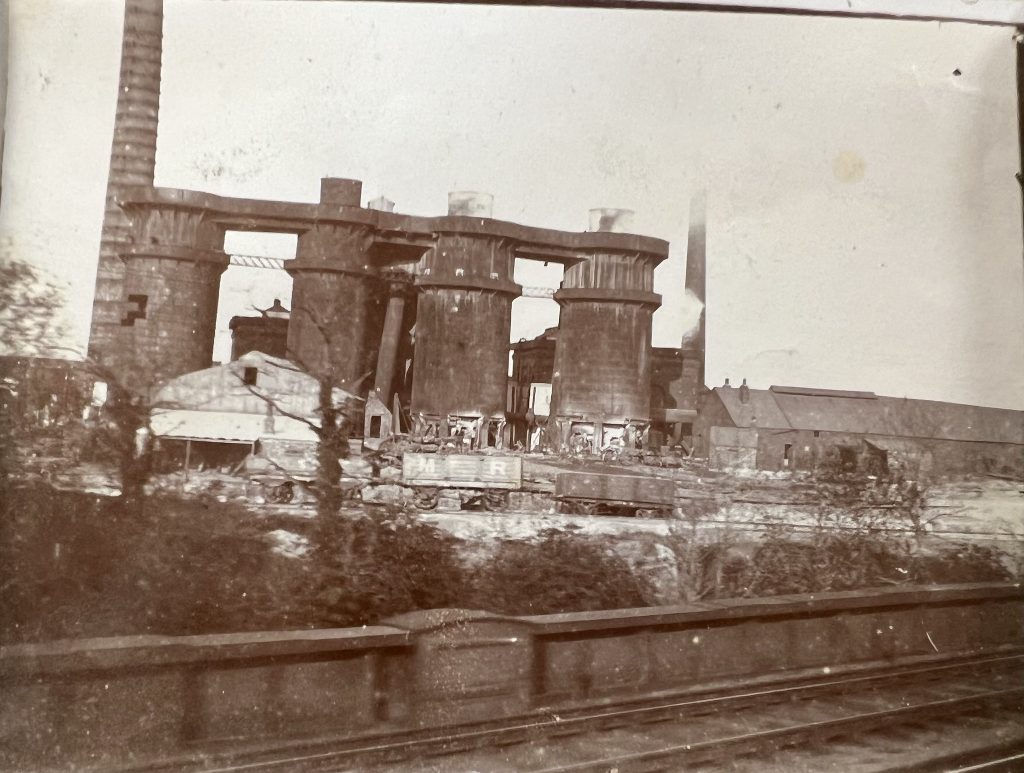
A early image of islip ironworks .
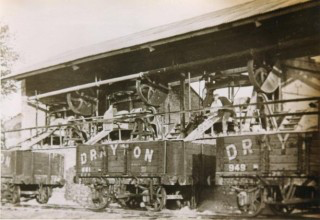
Here the 1m gauge system can be viewed, note the name Drayton on the wagons. photo from Thrapston History Society .
A common saying in the area “at Islip they made pigs & old men”
This was due to lifting the 2cwt pigs.
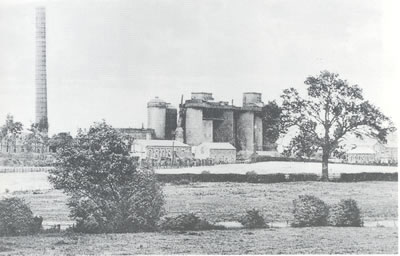
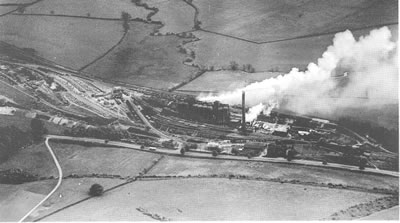
Construction of Islip furnaces started in 1871 by Charles Plevins, the first iron “pig” was cast on 20th April 1873. At this time there were only two furnaces, but business prospered, and in 1879 two further furnaces followed. Generally only three of the four was was at work, this was due to the other being often relined, most of the ore from opencast mining was used up by the furnaces by the turn of the century.
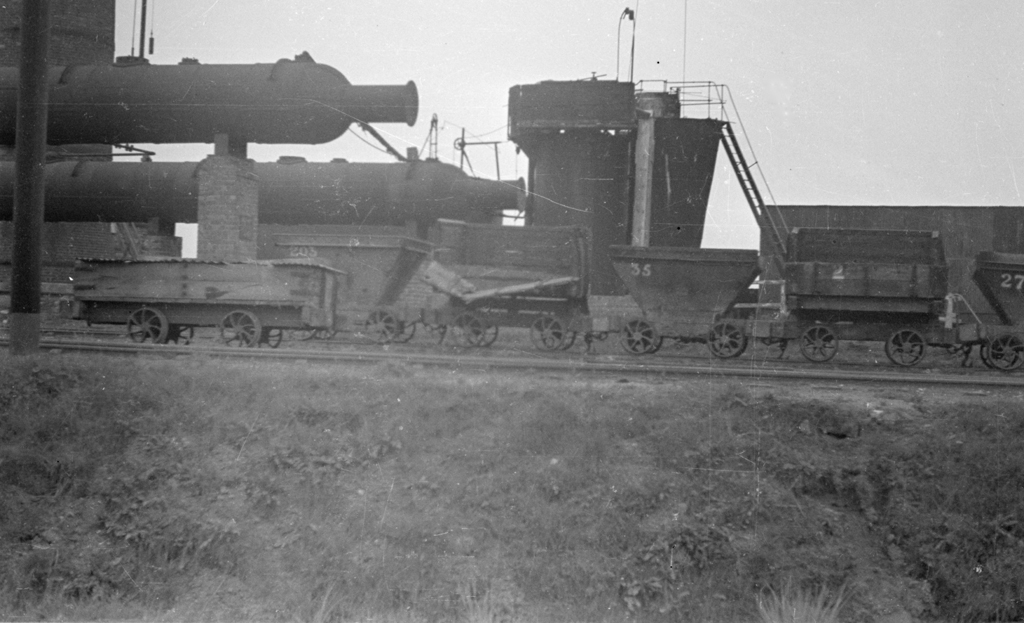
Various style wagons at the islip ironworks in 1948, possibly during the dismantling of the site . J R Foster-Smith collection ,Northamptonshire Industrial Archaeology Group.
Like many other companies in those days it was as near as self sufficient as it could be, many of these item requiring cast iron were made on site, including cast iron railway sleepers, barrow and wagon wheels. There was a comprehensive loco and wagon works where the tramway locomotives were overhauled and in some cases modified. Many of the hopper wagons were built and maintained here.
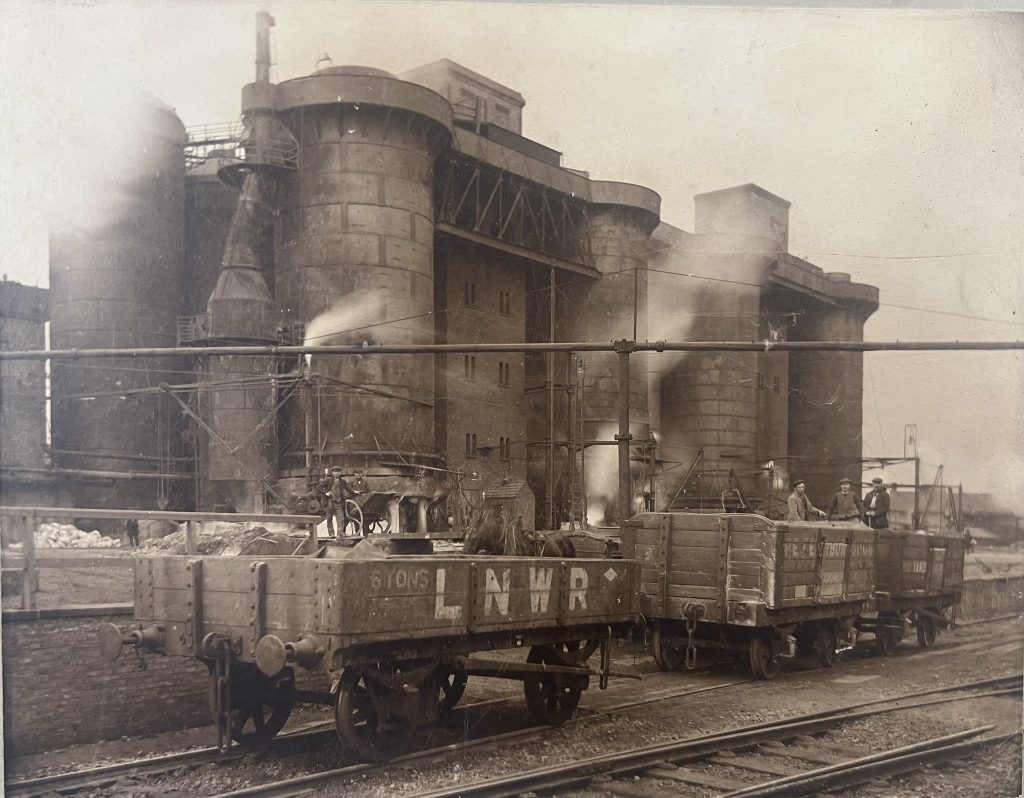
A early image of islip furnaces note the hand wheel barrows for loading and the horse at work.
Islip ironworks was of the first to introduce routine chemical analysis of the ores, and depending upon the results materials were weighed out before being loaded into the furnaces. As a result Islip iron was much sought after as being a high quality casting iron.
The system was very labour intensive with men shovelling ore, Calley, limestone or coke imp iron two wheeled wheelbarrows, which could hold 26cwt of ore. Some 40 of these were filled by man per shift. They where then wheeled via the weigh bridges, they were then laboratory assay reports, they might have to add extra or unload before taking to the lifts. Four wheel barrows were taken at a time up the lifts to the working platforms, which was 60ft up. Men where not allowed to travel up in the material lifts and so the team working on the platform at the top of the furnaces had to start or end their shift by a 60ft climb up exterior ladders.
They off loaded the barrows from the lifts and took them to the appropriate furnace and tipped there contents into the bell hoppers which were inside the circular cages on the working platforms. When the correct weight was reached a bell would sound the cage would lower into the furnace the materials would slide off , the counter balance weight was now greater pulling the cage back up, a plate would cover it to stop flames shooting up but the toxic gas would still escape.
During the war it was essential to keep the site hidden from enemy bomber pilots, the escaping burning gas was a problem, this escaping burning gas caused a problem at night it lit up the night sky. This surplus gas was allowed to lift an escape valve at the top of a small chimney on the working platform, and burn off. It was decided the best way to hide this was to erect a corrugated roofing over the platform and “pig” bays. The result of this was many of the men suffered the effects of gassing and extreme heat.
The furnaces lasted for nearly 70 years, the small bomb raid shelter still remains and 1 building which is used today as an office. The 185 ft chimney was felled on June 21st 1950.
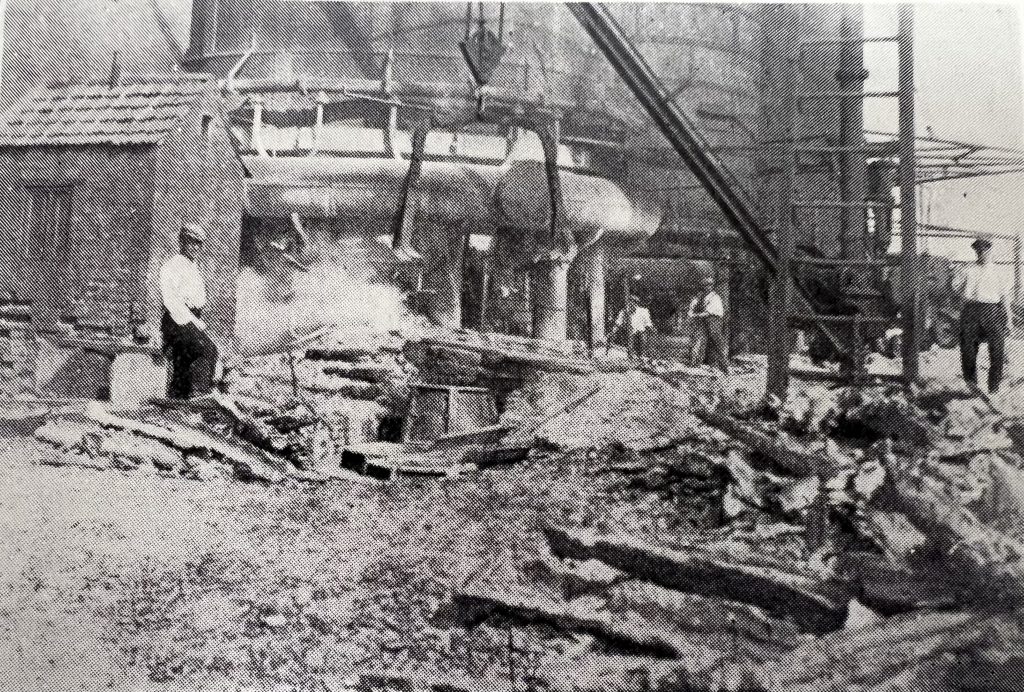
Molten metal pouring from the tower to the beds Islip furnaces
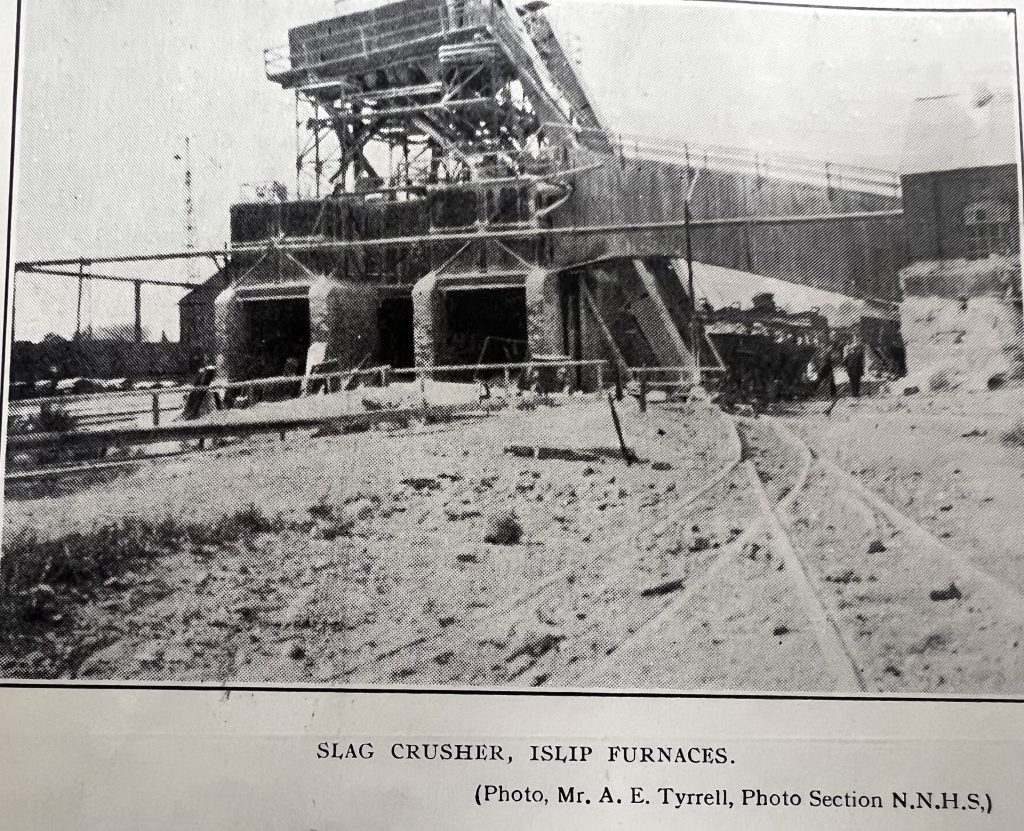
Wellingborough
In the beginning Wellingborough consisted of a small group of houses with a path to All Hallows church on the hilltop to the north; the ironworks lay to the east, surrounded by small open cast mines operated by horse drawn tramways, but there was no connection to the main line railway. This factor hampered development so much that Butlin built his Irthlingborough ironworks just outside the town of Wellingborough, with the convenience of railway access, commencing production in 1867; the old works was phased out and the area around it engulfed in the rapid expansion of Wellingborough in the late Victorian times. The new ironworks was in Irthlingborough Parish, as it lay on the east bank of the river Ise (hereabouts the parish boundary between Wellingborough and Irthlingborough) but geographically it was very close to the new town of Wellingborough, and is often referred to in early records, official correspondence and everyday conversation as Wellingborough ironworks; which has led to further confusion. In the account that follows therefore, we can only give such data as have been preserved or established, and leave some queries for local historians to unravel . In 1869 Butlin Bevan are given as operators this coincides with other dates for 2 more blast furnaces being added. The ironworks themselves where the property of Thomas Butlin and Co Ltd until taken over by United Steel ltd in 1920. The works later became property of the British Leyland group as Wellingborough foundries and closed in September 1981 .
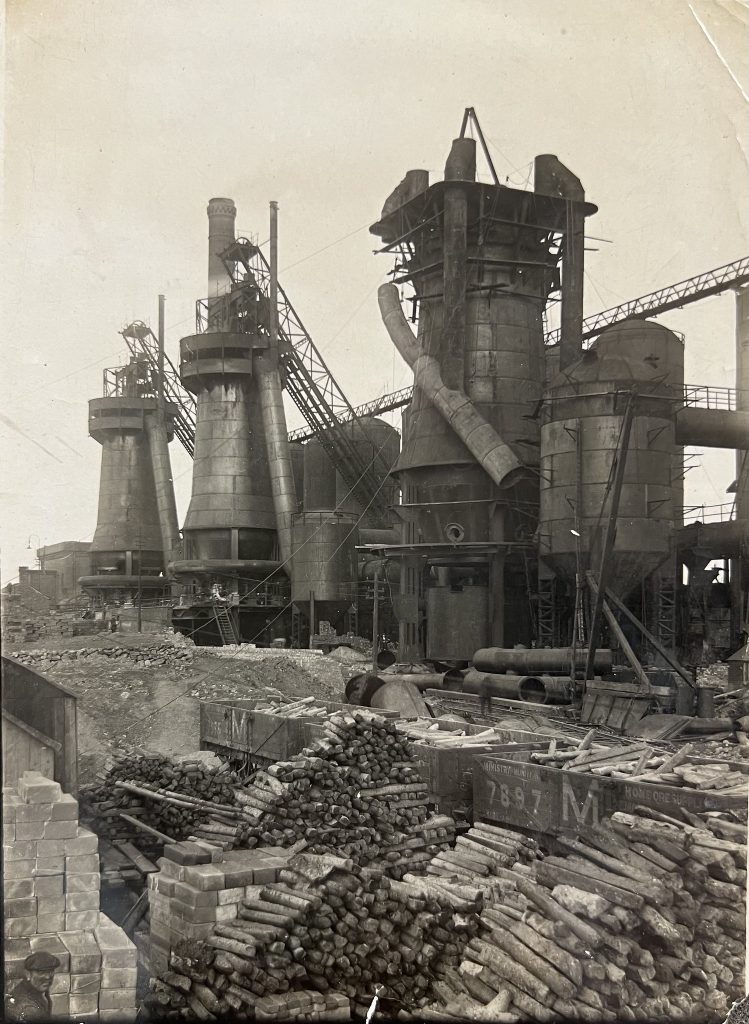
many timbers can be seen in the foreground of this image, Along with kiln bricks .
The East End works were the first ironstone works to be built actually in the Northamptonshire ironstone field; the exhibition of samples of ore from the county at the great exhibition of 1851 encouraged Thomas Butlin to erect an experimental furnace at Northampton and afterwards- following the discovery of sustainable beds of ironstone in the neighbourhood of Wellingborough and Higham Ferrers – to build his East End works under the style of Thomas Butlin & co. The first furnace was put into place in June 1853 and was fed with ore garnered from the immediate vicinity, testified by the sunken areas in the neighbourhood of Finedon road, and now occupied by parks and allotments; on the north side west of Cross road, and on the south side of Nest Lane.
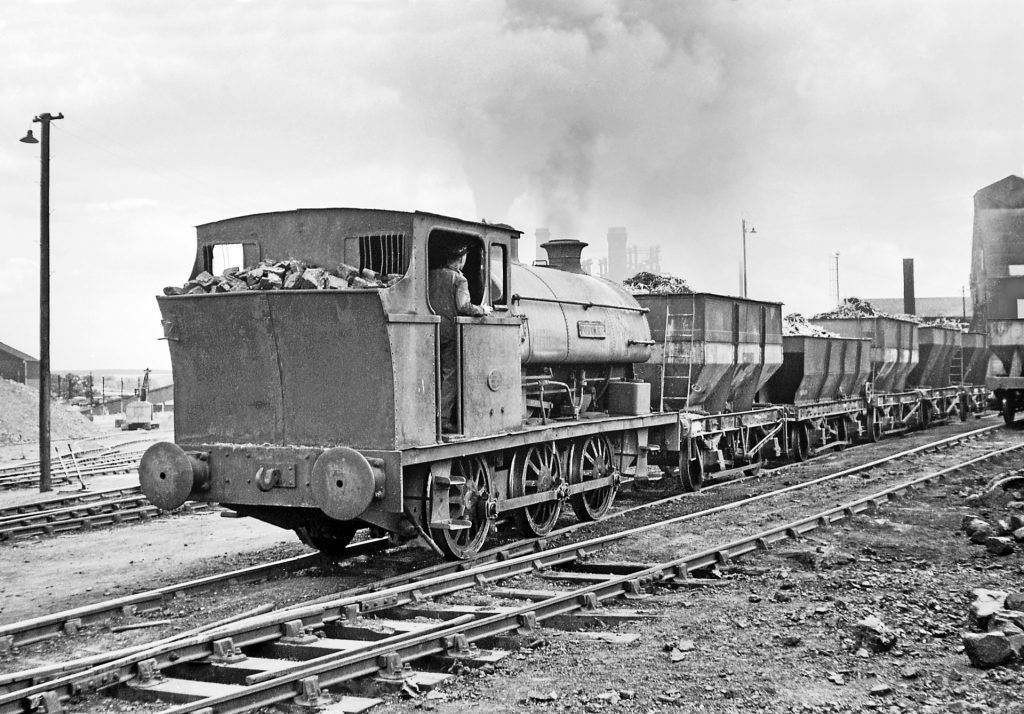
photo by Gordon Edgar
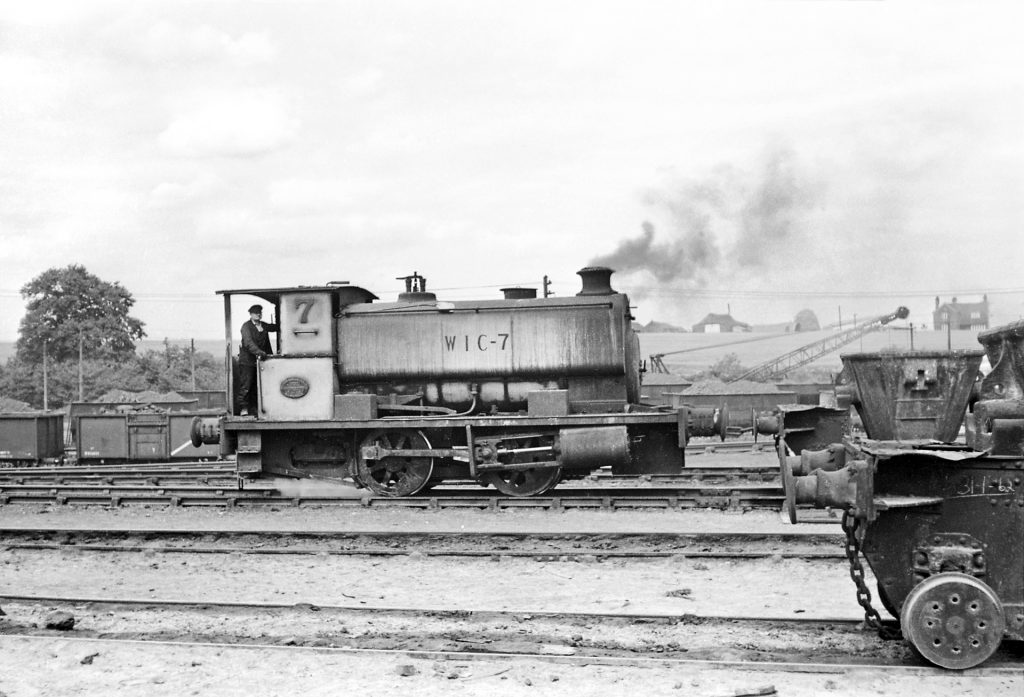
photo by Gordon Edgar
The below image is a glass slide , this was scanned by Northampton archive centres. It shows wellingborough iron ore sidings.
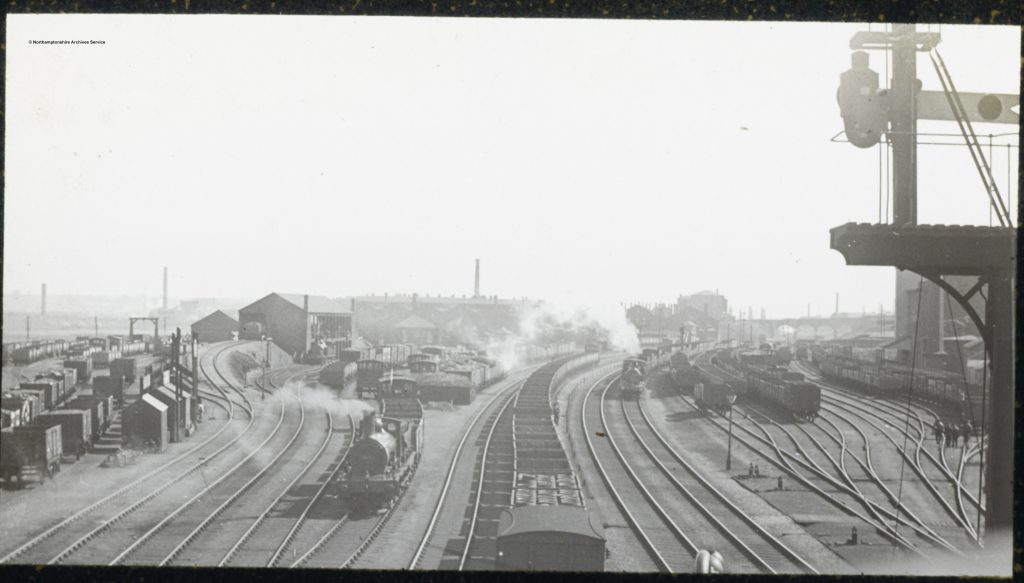
Corby
The very first corby steel works was introduced in 1910, These where the largest of the steel works in Northamptonshire & some sections still remain today. In 1910 the plant passed to Stewart and llyods as a subsidiary of Alfred Hidsom . The company purchased the site in 1920 , Stewart and lloyds was by far the biggest mining operation in the midlands, other mines was active but these typically sent there ore to there own furnaces .
useful information & videos
https://www.bfi.org.uk/features/corby-steel-town
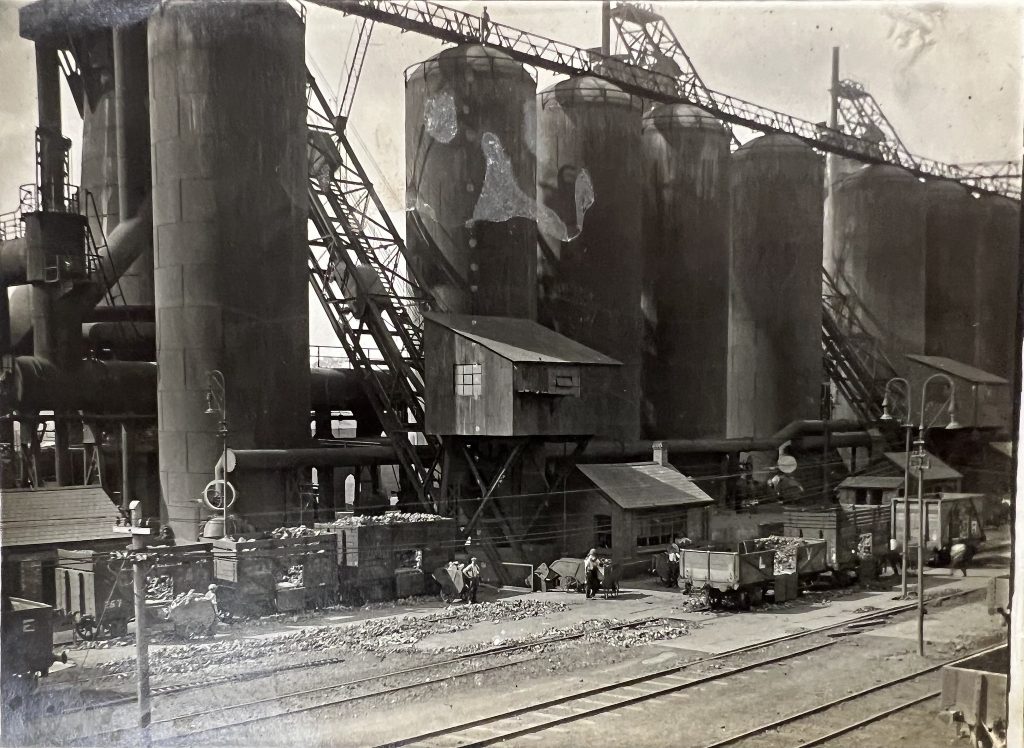
Multiple stoves and skip hoists can be seen in the image above.
Ore preparation plant:
The objective for an ore preparation plant is to prepare for the blast furnaces an iron bearing mixture which is, as far as possible ,of s constant composition. The mixture is not only ironstone but contains other waste products from various parts of the site, which by virtue of their iron content, make their incorporation into there iron ore content worth while Crushing plant The crushing plant at the Corby steel works was very large, ore from the local mines & surface mines got brought in 20 x 5 ton railway carts. These was weighed on 42 ton tippler weigh bridges , this passed the ironstone onto the primary crusher where rollers crushed the ironstone into smaller more uniform range of sizes . This ore is then sent along a conveyor belt to a 2nd smaller nobbly crusher, this crusher would make the ore much more suitable for the blast furnaces later on . The ore now is dropped onto underground conveyor belts which would take it to the ore preparation beds. It is worth mentioning ore from various mines and surface mines would get mixed up as contents varied, some places had higher contents of certain things .
Ore preparation beds:
The ore now is sent again on a conveyor belt, this feeds a wing tippler machine which lays the ironstone in long heaps , flu dust , mill scale etc are fed into the conveyor at this stage also to create the correct mixture. When these sections are roughly 3000 tonnes a reclaimer recovers these in strips and pushes the correct amount down a further conveyor . From here everything is mixed and screened for the final time .
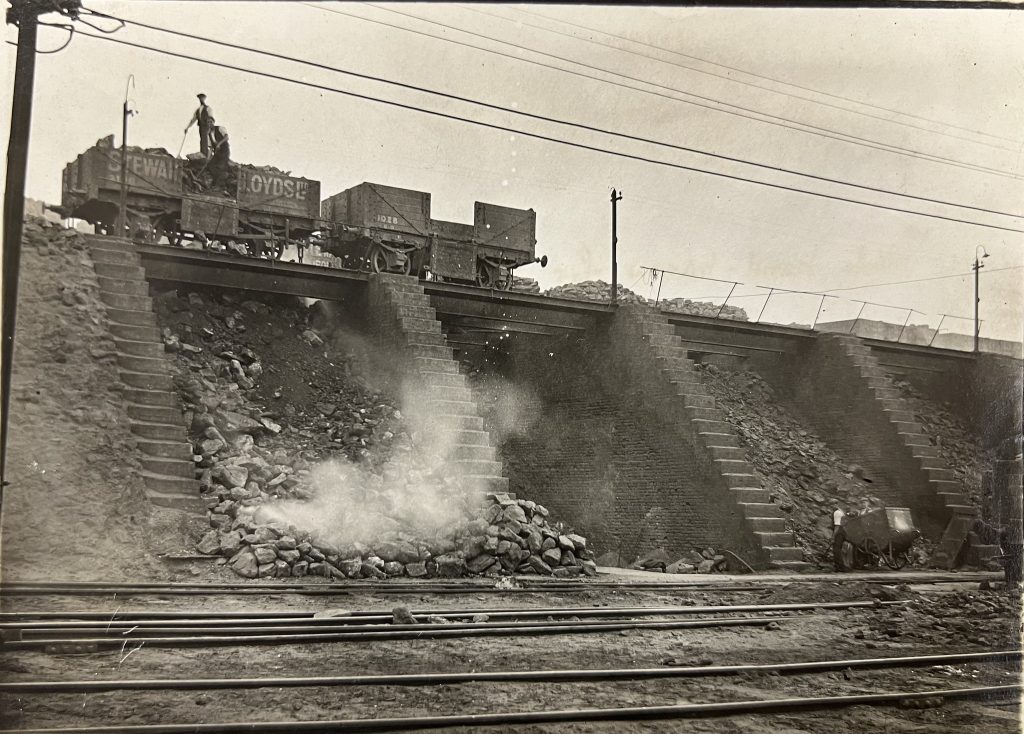
Ore boys at work in the ore pays opposite the furnaces , notice the hand barrow middle right for skip charging.
Sinter plant:
The process of the sinter plant is to agglomeration the fines to a suitable form for the blast furnaces , if this process didnt take place the fine dust would choke to furnaces . It has become more and more a pre digestion process of materials for the blast furnaces , with the ultimate possibility of producing a 100% self fluxing sinter burden .
The sinter itself is a complicated mixing area where coke- water-pressurised air ducts – cook the mixture from the top downwards , from here again it’s moved to a conveyor belt , to go on its last journey to the blast furnace .
Blast furnace
The ore was at the end of the process now, limestone ,iron ore ,coke was dropped into the furnace through a hatch in the top. At the bottom of the furnace warm pressurised air was forced inside to increase the temperature to extreme heats. The lining of the blast furnaces was constructed of fire bricks to be able to withstand the extreme heat, water is pumped inside the jacket to maintain a constant temperature . From here the liquid iron would exit through a drill hole in the very bottom, slightly higher up the slag would exit through a separate hole . Now the iron would be aloud to go into moulds to create the pigs once cool .
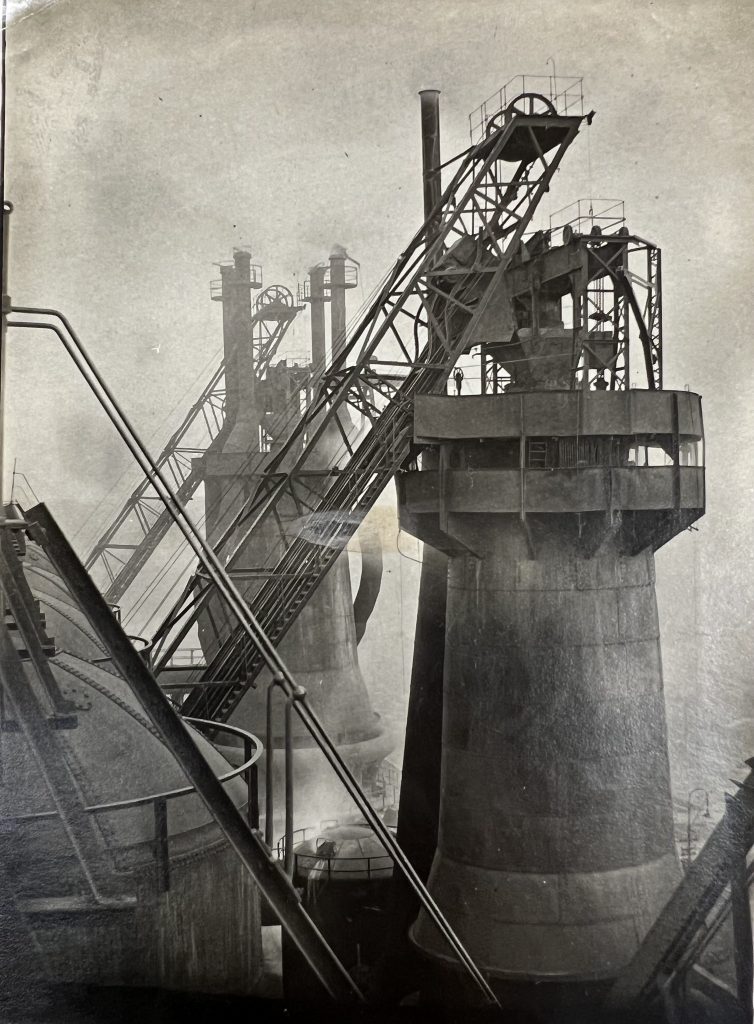
The no 3 furnace at work .
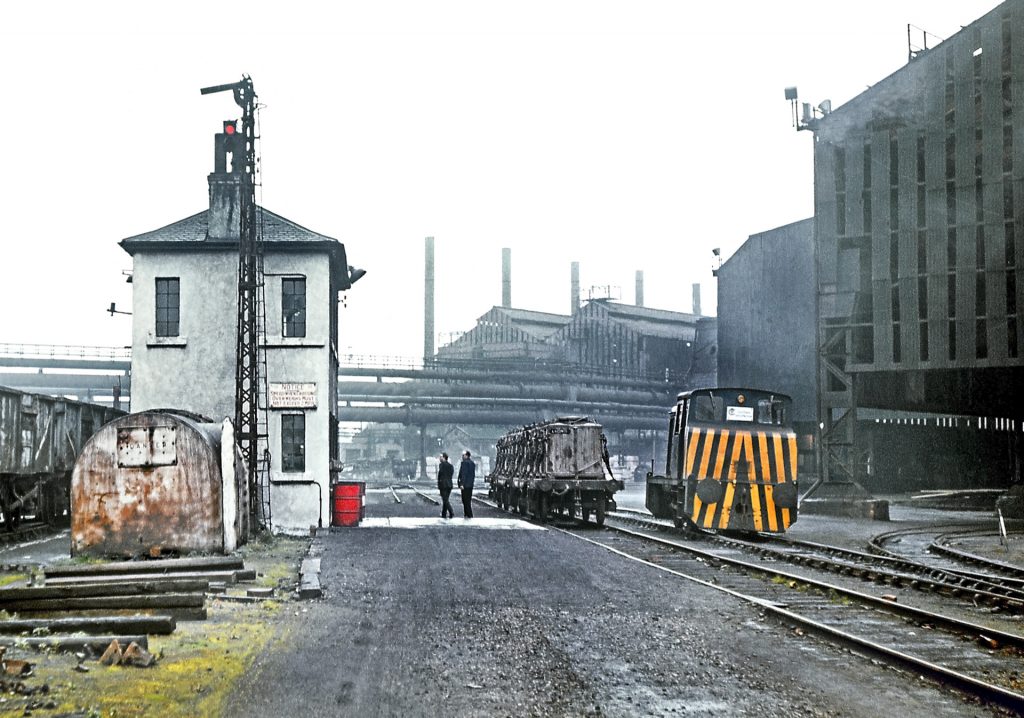
photo by Gordon Edgar
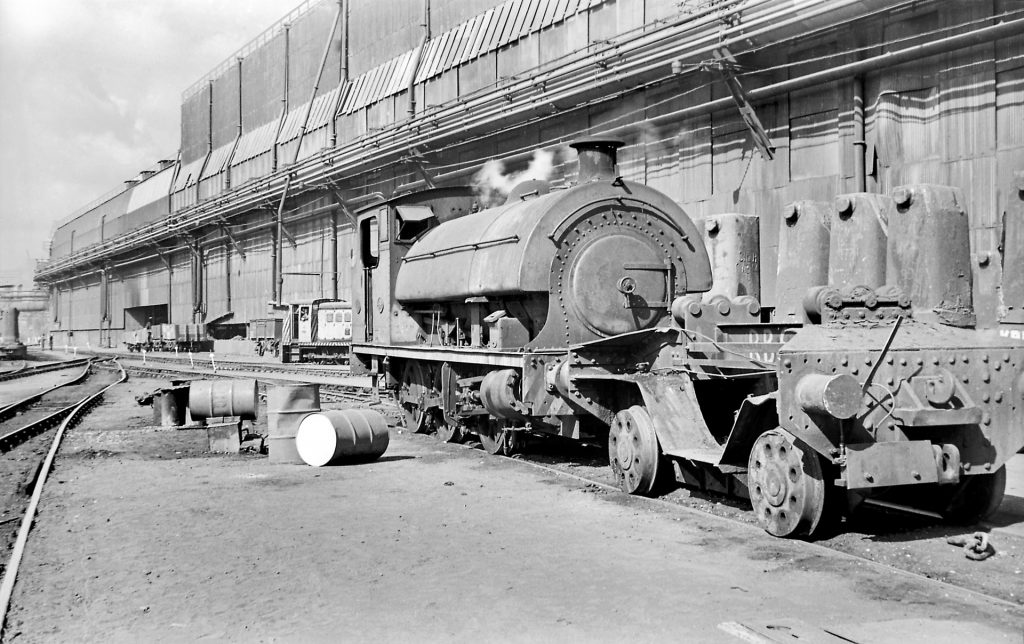
photo by Gordon Edgar
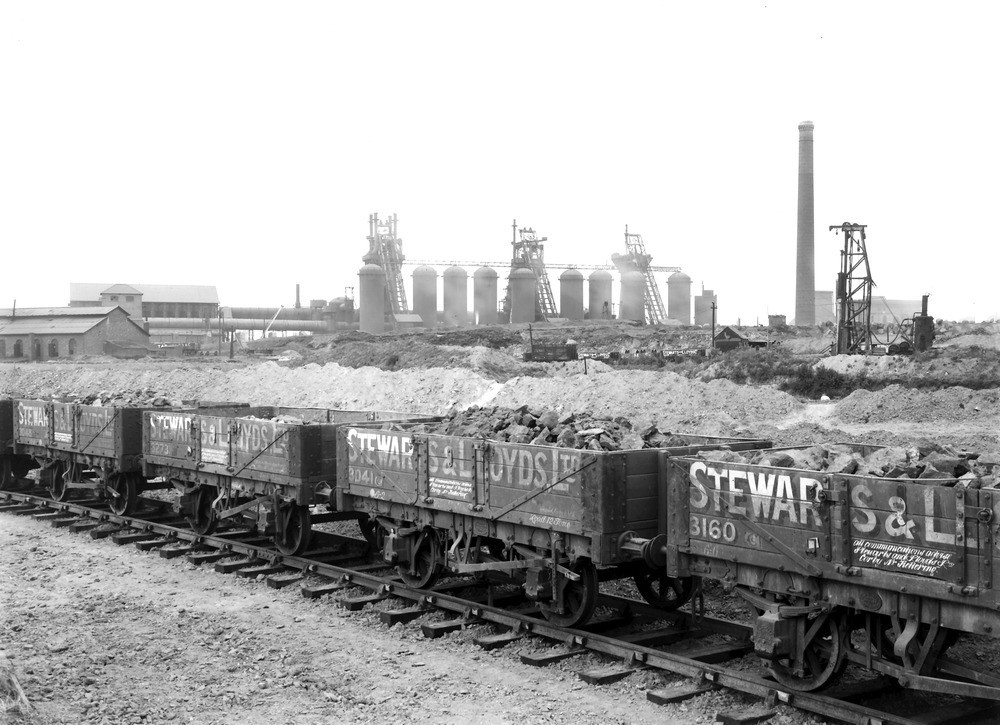
Stewart and Lloyds Ironstone Works, Corby. Looking NW. General view of blast furnaces and stoves. 1933 BGS archive
The day of demolition .
https://www.macearchive.org/films/atv-today-06111981-corby-steel-works-demolished
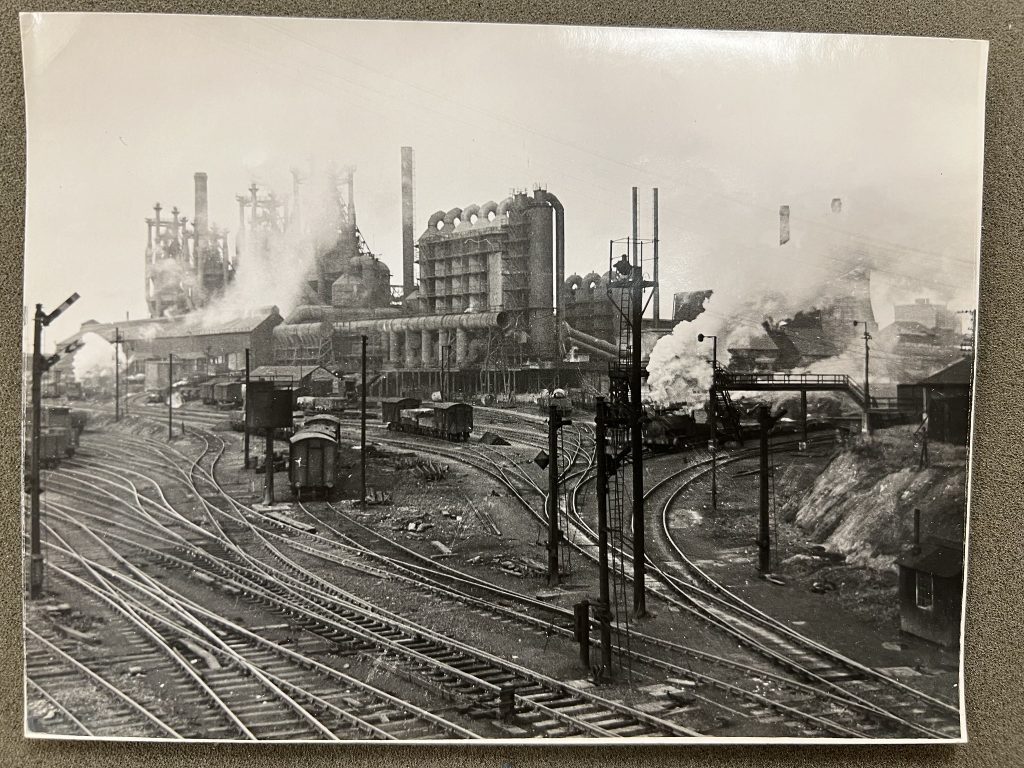
The loco in the above image really does make it feel alive.
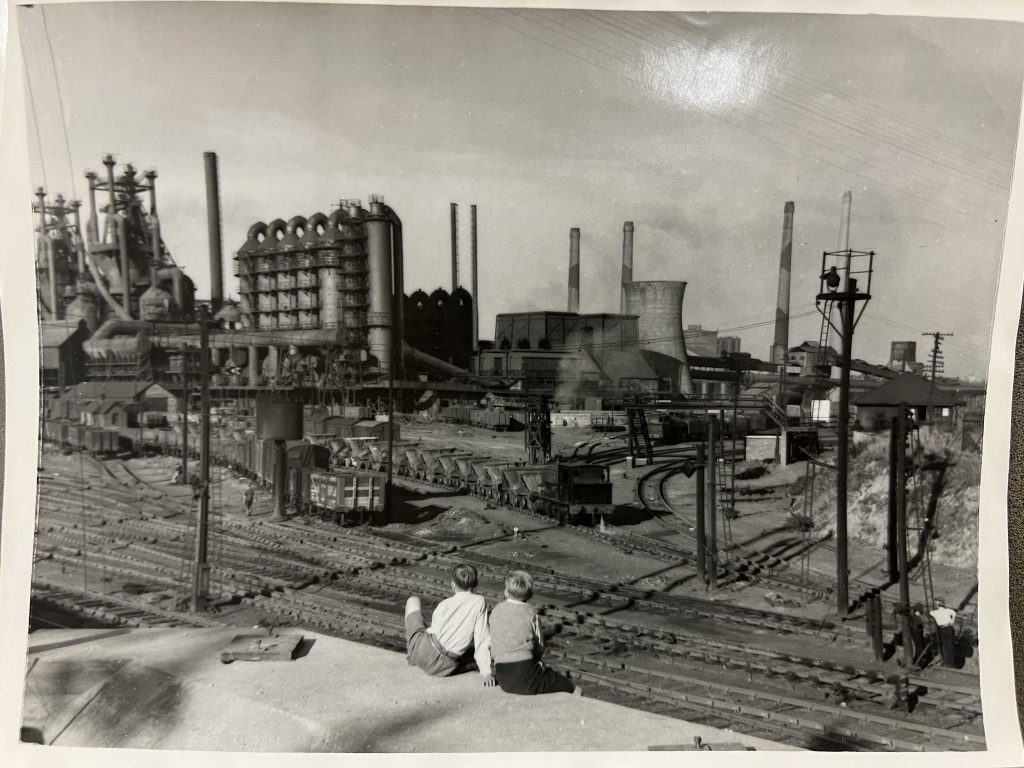
More pictures from Corby smelting works are here